-
Course Code
ISOM-007
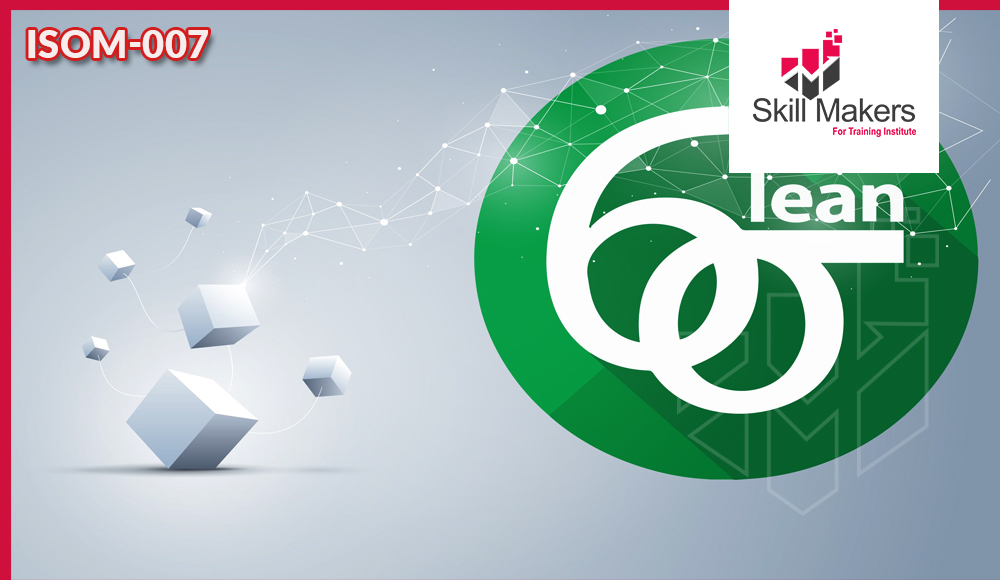
Lean Six Sigma Black Belt
- Six Sigma is a world-recognized credential for quality and process improvement. IASSC (International Association for Six Sigma Certification) is the certification body that defines standards for Lean Six Sigma methodology, and tests capabilities on Lean Six Sigma body of Skill Makers . Through different levels of certifications – Yellow Belt, Green Belt and Black Belt, individuals can demonstrate Skill Makers of sustained quality improvement through continuous efforts. Acquiring a certification validates an individual’s/company’s ability to comply with the rigorous standards as defined for every level.
- Six Sigma certifications impart skills for different phases of DMAIC cycle (Define, Measure, Analyze, Improve, and Control) and problem-solving processes in order to save time and money, and in the process, improve performance to a great extent.
Learning Outcomes
- Participate in the development of a successful Six Sigma program
- Contribute to the definition of project selection criteria and develop project proposals to meet those criteria
- Lead a Six Sigma project team using the DMAIC problem-solving methodology and team-building skills
- Ensuring compliance with quality standards
- Enhancing leadership ability and growth/promotional prospects in companies
- Describe the quality in terms of product features and freedom of deficiencies
- Identify external and internal customers
- Describe yellow belts, green belts and black belts
- Apply and interpret basic and advanced Six Sigma tools, as necessary, for project definition, process baseline analysis, process improvement, and process control
- Demonstrate your skills in an industry-recognized certification exam
Course Contents
- Six sigma and organization Goal
- Lean Principles in the organization
- Design for Six Sigma in the organization
- Enterprise view
- Leadership
- Organization Goal and Objectives
- Foundation of Six sigma
- Business process management
- Voice of customer
- Business Results
- Project Management
- Lean Principle in the Organization
- Process management for projects
- Project management Basics
- Management and planning tools
- Business Results for projects.
- Team Dynamics and performance
- Project Matrices
- Problem Statement
- Process Analysis
- Probability and statistics
- Collecting and summarizing Data
- Probability Distribution
- Metrology
- Process Capability of attribute data
- Measurement system Analysis
- Process Capability and performance
- Exploratory Data Analysis
- Hypothesis Testing
- Design of Experiment includes
- Terminology
- Planning and organizing experiments
- Design Principles
- Design and Analysis of One Factor experiment
- Design and Analysis of full factorial experiments
- Design and Analysis of two-level fractional experiment
- Taguchi Robustness Concepts
- Mixture Experiments
- Statistical Process Control (SPC)
- Implement and validate solutions
- Control Plan
- Project Presentations
Section-1: Overview and History of Six Sigma
Section-2: Define
Section-3: Measure and Analyze
Section-4: Improve & Control
Our Methodology
- Make coaching and monitoring innovative and using modern
- Media training also using on the go training by using interactive means and focusing on
- The exercises, practical applications and real situations study
- Live delivery method, instructor-led training
- Experienced consultant, trainers, and professional
- Qualified trainer with high-level experience
Attendance Reports
- Send daily attendance reports to training departments
- Send full attendance report to training dep. by the end of the course
- Attend 100 % from the course days also provide daily
- Issue attendance certificate for participant who attend minimum 80% from the course duration
Pre/Post Reports
- Pre- assessment before starting training
- Post assessment after finish training
- Full report for the deferent between Pre-& Post assessment
Who Should Attend
- Senior Management
- Team leaders
- Software Professionals
- Project Managers
- Quality Assurance Managers and Engineers
- Software Quality Assurance team members
